Sumi
Uchigai Enamel 4.2 Tea Bowl / 内外網絵4.2茶付
Uchigai Enamel 4.2 Tea Bowl / 内外網絵4.2茶付
Couldn't load pickup availability
Ф126*h62
・Arita Ware Porcelain produced in the vicinity of Arita town in Saga Prefecture. Arita Ware, made by Korean potters who migrated to Arita in the late 16th century, is famous as the first porcelain produced in Japan. Over the past 400 years, it has been used not only as daily necessities but also as decorative items. Some exceptional pieces of Arita Ware were even offered to the imperial family. Despite its delicate appearance due to being thin and light, Arita Ware is known for its durability, being considered more robust than regular pottery. Additionally, its fine and smooth texture is achieved by mixing magnetic soil and stone powder. The white base is suitable for painting, and the delicate and vibrant painted decorations are particularly charming.
・Hasami Ware Ceramics produced in Hasami town, located near Arita town in Saga Prefecture, where Arita Ware is also produced. With a history of over 400 years, Hasami Ware boasts about 16% of the market share in daily tableware even today. The "Kurawanka Wan," a sturdy and unbreakable bowl with a painted arabesque pattern, is a representative work of Hasami Ware and is beloved by many pottery enthusiasts. The distinctive features of Hasami Ware include the beauty of white porcelain and the delicate underglaze painting technique using the Wu Su (indigo) color. Evolving with the times, various daily tableware items for the common people have been created while continuously improving the craft. Hasami town remains the largest kiln industry area in Nagasaki Prefecture, and its shipment of Japanese tableware ranks third nationwide.
・Manufacturing Process STEP1 Forming (Seikei) Create a clay with stickiness from porcelain stone and shape it. There are mainly two methods of creation: "potter's wheel forming," where clay is placed on a rotating table and shaped by hand, and "casting forming," where clay is poured into a mold.
STEP2 Bisque Firing (Suyaki) The formed items are dried in the shade and then fired at about 900°C. Firing makes them more durable and facilitates painting.
STEP3 Outline Drawing (Shitaezuke) Perform "line drawing" to outline the pattern or apply "noumi (dummy)" during line drawing.
STEP4 Glazing (Seyu) Applying glaze on top creates a glass-like thin film when fired.
STEP5 Final Firing (Honyaki) Bake at a high temperature of 1300 degrees. There are three firing methods: "bake firing," "attack firing," and "fry firing." "Sometsuke" (underglaze blue), "white porcelain," "seiji" (celadon), and "ruri" (cobalt blue) are considered completed after the final firing.
STEP6 Overglaze Painting (Uwaezuke) Color is added to the fired items using colored glazes.
STEP7 Final Firing (Shosei) To fix the colors, bake at 720 to 830 degrees, completing the process.
Share
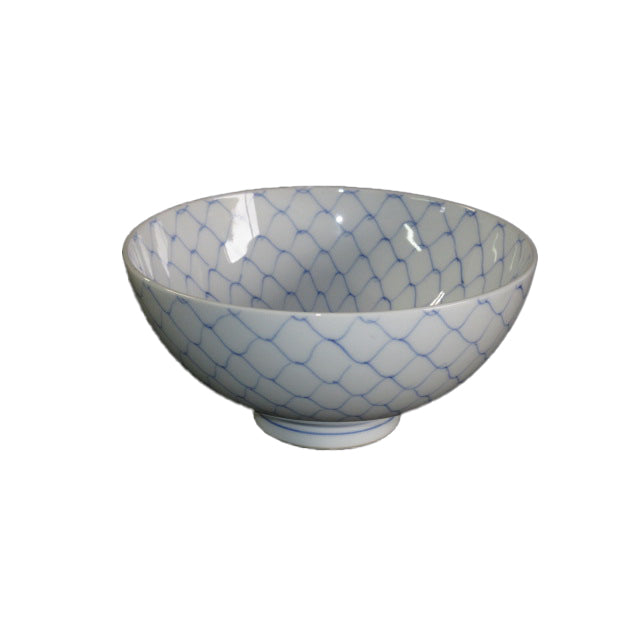